All my pieces are sand cast and handmade by myself in-house. Sand casting is an ancient technique whereby I create a mould using petrol bonded sticky sand that I can then pour molten recycled silver or gold into. I use a two part flask made from two aluminium rings that fit together and line up perfectly. Once I've set up one half of my mould with compact sand I use talcum powder to dust the surface of the sand and the piece I'm casting so it doesn't stick as I push it into the sand. I then line up my second ring and fill it with sand and hammer it down to ensure a tight mould.
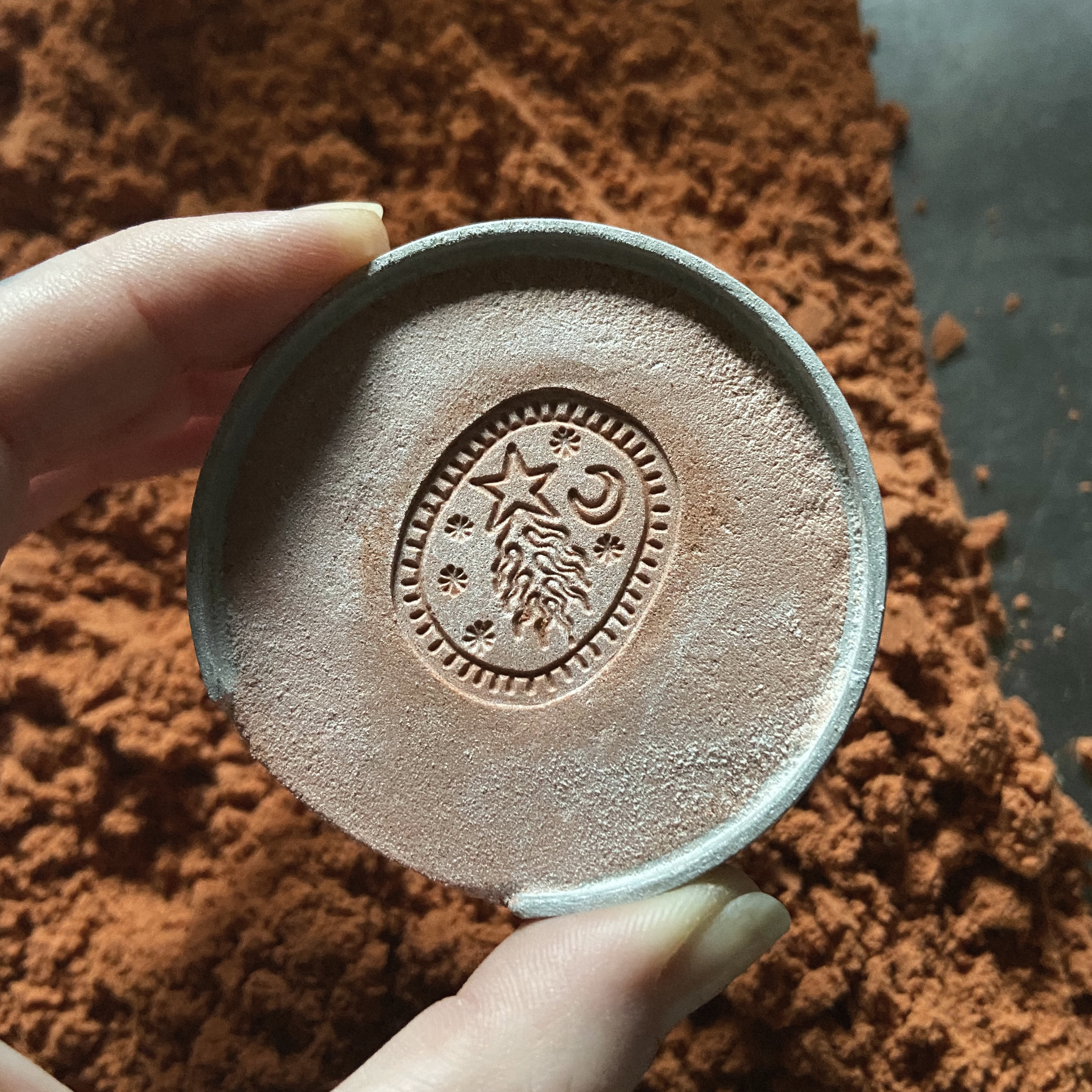
I carefully part the mould and remove my casting piece, I'm left with two halves that go together to create the whole piece. I now need to carve out a pouring tunnel for the molten silver to flow down into. Depending on the size of the piece I will also make some air vent holes around the mould to make sure the silver flows into every part properly.
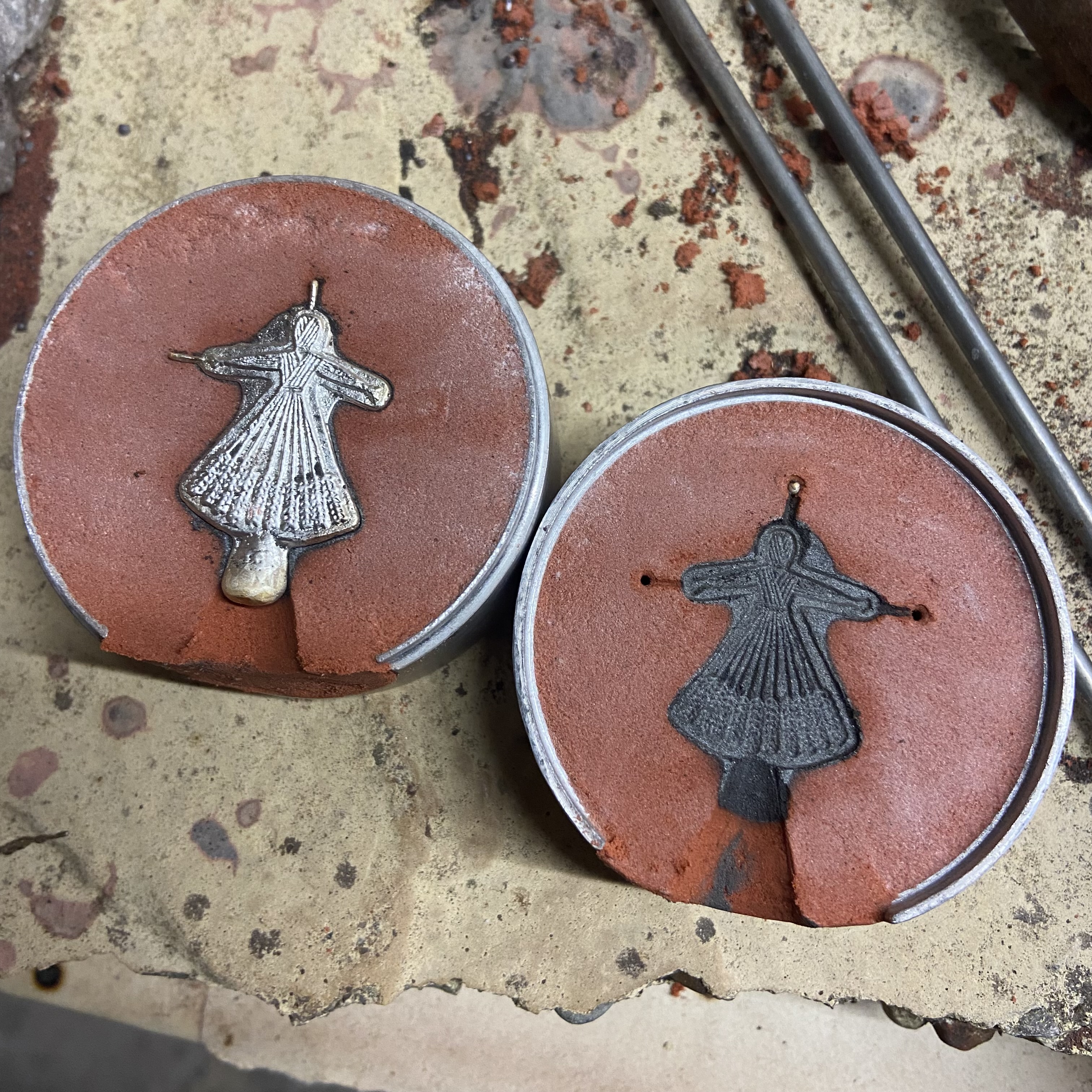
It can take me approx 30-40 minutes to prepare one mould and 10-15 minutes to pour the silver or gold. I only use the mould once as the sand is left dry and burnt after pouring and you lose detail. There's no guarantee the cast will come out as intended, there's lots that could go wrong and not every cast is successful but I've learnt from mistakes over time.
Once I have a cast piece I'm happy with, it’s now time to trim, file, solder on jump rings before sanding and polishing all by hand. It could take me between 1-8 hours to do all this depending on the piece which does not make it a fast process and it doesn't always come out as expected but that's why I love it so much. You get unique casts each time, giving the jewellery its own characters.
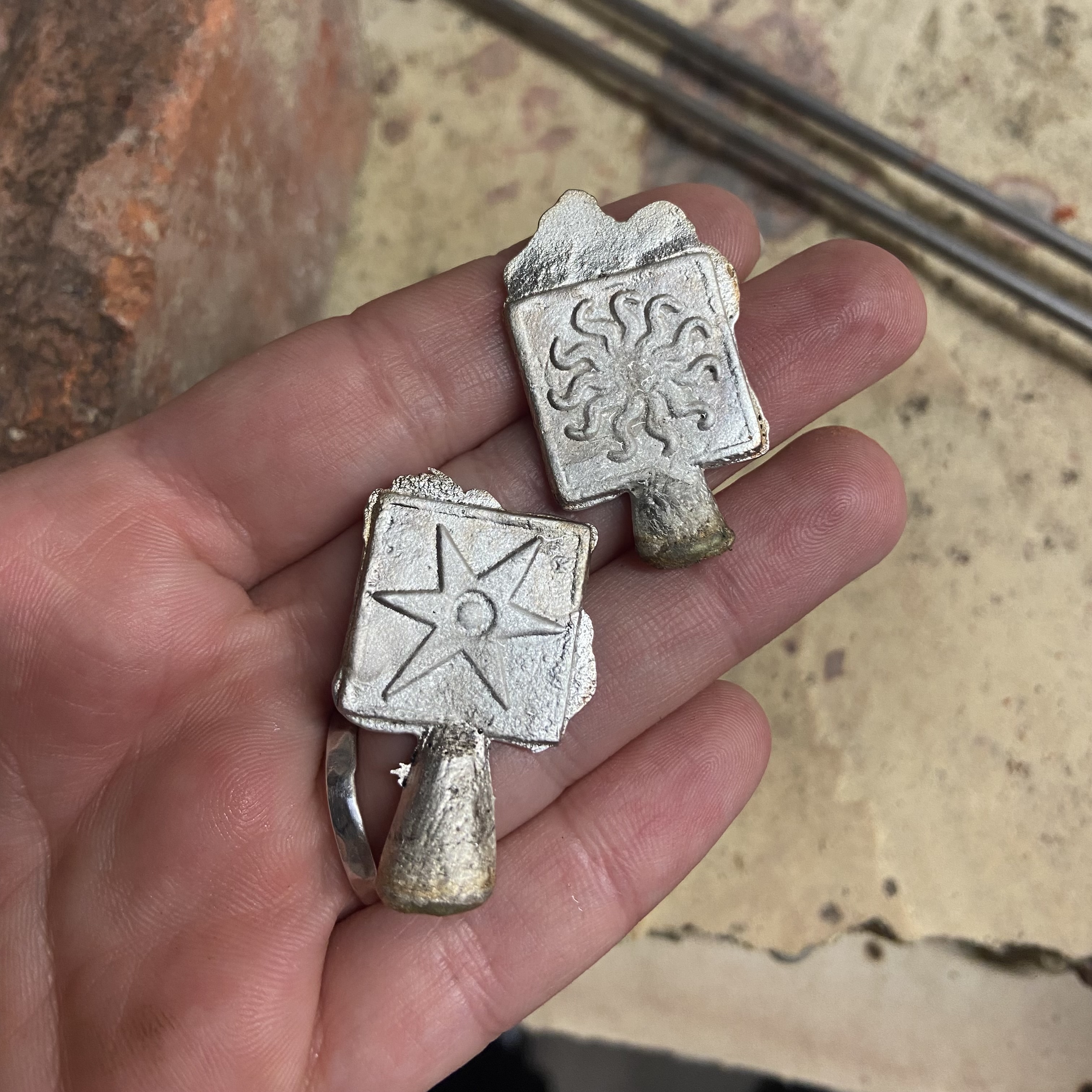
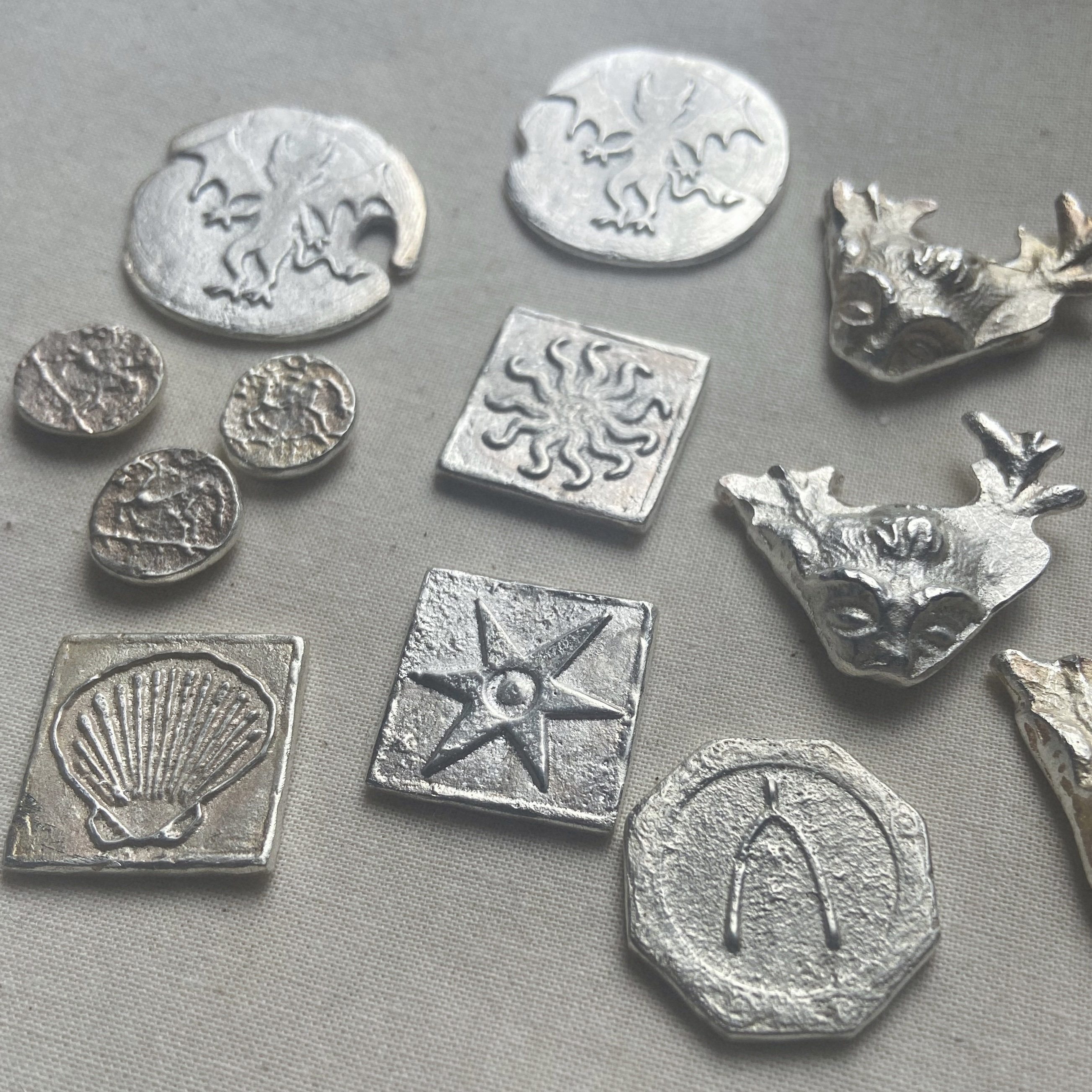